Robotic Spring Manufacturing
- Originally published by Newcomb Spring
Newcomb Spring Implements Robotic Automation, Improving Efficiency and Precision
The International Federation of Robotics forecasts that by 2019 1.4 million industrial robots will be installed in factories around the world. Manufacturing organizations are looking to this technology as a way to streamline operations, improve safety on the factory floor and grow their business. Newcomb Spring Corp., one of North America’s largest custom spring, wire form and metal stamping manufacturers, has been at the forefront of innovation in their plants, adding proprietary and purchased technologies to their arsenal. Recently, Newcomb Spring added robotic automation to its operations as part of the company’s continued effort to improve efficiency and quality.
The UR3 tabletop robot was recently introduced at the Newcomb Spring of North Carolina facility and is currently affixed to a Wafios® FMU CNC wire forming machine. Considered a “collaborative” UR robot, also known as a cobot, the UR3 is part of an emerging class of robots that some industry experts predict to be the largest market driver of industrial automation.
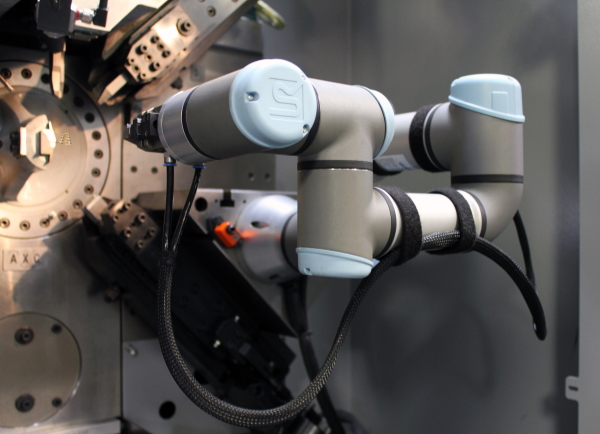
Designed and built by Universal Robots, the UR3 is a tabletop robotic arm that is capable of light assembly tasks and automated operations. With six jointed connections that provide 360-degree rotational movement, the unit is capable of handling products up to 6.6 pounds (3 kg) and reaching up to 19.7 inches (500 mm). The UR3 requires minimal space on the manufacturing floor and can work alongside people without safety guards, due to built-in systems that automatically stop the robot’s arm if it encounters an object or person in its path.
Newcomb Spring selected the UR3 for its ability to support employees by performing repetitive operations quickly, consistently and precisely. While primarily used for spring and wire form product sorting and packaging, the unit can complete a variety of tasks in assembly and production. The robotic arm has been implemented as a collaborative tool that reduces human fatigue and errors and increases overall productivity by running 24-hours a day. This allows employees to complete projects rapidly and focus their time on other areas of production.
“Newcomb Spring prides itself on a culture of continuous improvement,” says Keith Porter Jr., General Manager of Newcomb Spring of North Carolina. “We are always striving to find new ways to better our processes and value. The UR3 is an excellent tool for precise tasks, and the machine’s programming allows it to be re-deployed for a variety of efforts, and to deliver consistent results.”
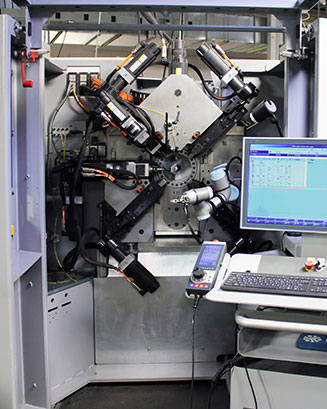
CrossRobotics, an integrator of UR robots, worked with Newcomb Spring to implement the UR3. According to Grady Turner, Applications Specialist with CrossRobotics, the UR3's ease of use allows for very quick reprogramming for different parts and different machines.
Recently the UR3 was utilized on a high-volume production run of beryllium copper battery contacts. The robot was programmed to remove the component from the FMU and place it in a molded plastic tray. The precise movement of the robot provided accurate positioning and timing, allowing the robot’s gripper to grasp the parts’ complex geometry - without causing damage to the springs or creating pressure on the feeding wire - holding the battery contact just as the wire was cut. As the FMU began to coil its next component, the UR3 arm rotated and moved, placing the battery contact on a nearby plastic tray. The UR3 then returned to the FMU to collect the next part just as it was completed.
The UR3 was programmed to place parts in different cells of the plastic tray, progressing until the entire tray was filled. A Newcomb Spring employee then loaded in a new, empty tray without interrupting production. The company noted that the robotic arm improved efficiency by reducing part handling and increasing production output, because the equipment could run for long, uninterrupted periods while employees performed other tasks. In addition to loading the plastic trays, Newcomb Spring staff were often able to monitor other machines, reload wire into the FMU, conduct quality checks, and pack the filled trays into shipping boxes as spring manufacturing continued.
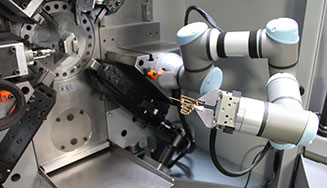
“By reducing part handling, as well as allowing our staff to be more productive, this robotic technology streamlines our operations,” continued Porter. “It’s a great advantage for high-volume jobs, and allows Newcomb Spring to continue to provide the highest quality components and best value to our customers.”
“Integrating new technologies has been a long-standing dedication at Newcomb Spring, and we recognized that this type of robotic system would provide a variety of benefits,” continued Porter. “Employees are excited about the UR3, because it helps them to increase output and eliminates routine tasks. From a management perspective, the UR3 provides quality and efficiency. Newcomb Spring of North Carolina is excited to highlight our successful use of the UR3 as additional Newcomb Spring facilities integrate the technology.”
Learn more about our custom spring and metal forms, or contact a facility near you today to discuss your custom manufacturing needs.
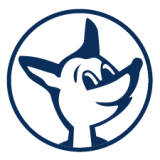