Titanium Alloy Spring Capabilities
- Originally published by Newcomb Spring
Considering the Advantages of Titanium Alloy Springs for Lightweighting Applications
Across a wide range of markets and products, today's design engineers face the same instructions: "Make it lighter, smaller, and more efficient." From making aerospace vehicles and transportation equipment more fuel-efficient to microelectronics used in leading-edge wearable technology and portable medical devices, manufacturers are looking to reduce weight, conserve energy, and optimize space.
With springs playing a vital role in so many products, engineers need spring design solutions that comply with today's trends for smaller, lighter products, while still delivering optimum performance. Material substitution is a standard way to begin addressing weight reduction issues. Substituting titanium alloy springs for more conventional steel springs provides many advantages in weight, size, and performance, but also calls attention to some important considerations.
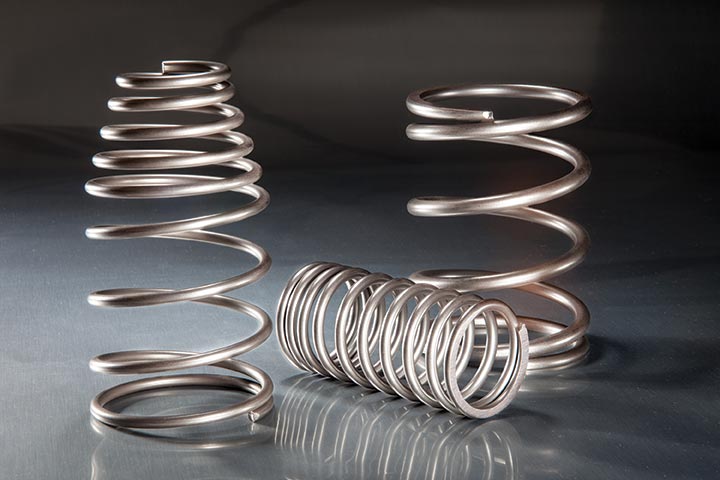
Steel alloys are the most common spring manufacturing materials. However, when it comes to lightweighting, titanium springs are typically up to 70% lighter than steel equivalents. Titanium is less dense and also has a lower shear modulus than steel, approximately two times lower, making titanium twice as "springy" as steel. Spring deflection for titanium springs is also higher than steel springs, meaning titanium springs require less active coils than comparable steel units. By using titanium, designers can reduce spring free-height, saving space and weight without sacrificing performance.
Regarding performance, titanium also offers some unique advantages. Because titanium springs are lighter and less dense than steel springs, they have lower mass and therefore require less energy to accelerate and decelerate each time the spring moves. Lower mass and energy requirements reduce spring surge in working conditions and result in a smoother and more controlled motion under load. These performance advantages are particularly noticeable in vehicles such as motorcycles and mountain bikes, where compared to steel, titanium springs reduce wheel hop over bumps and rough terrain.
Titanium's characteristics allow engineers to use a larger wire diameter but fewer coils to provide a spring rate that is equivalent to the rate of the steel spring being swapped-out. Titanium is lighter and more controlled, and it reduces space requirements. Add to this titanium's high corrosion resistance, and you have material worthy of consideration for a wide range of applications where weight and space are critical parameters, especially for applications in harsh environments.
The Disadvantage of Using Titanium: The Outlook is Changing
Titanium is only about 75% as strong as steel. While this is a consideration for heavy-duty applications, engineers can compensate, to some degree, by increasing the wire diameter of their titanium springs. Titanium's long-term wear-resistance is also not as high as the wear-resistance of steel, but methods such as anodizing can increase surface durability. The biggest drawback to specifying titanium alloys is cost. Traditionally, titanium is expensive. It can cost up to 6 or 7 times more than steel.
The good news for titanium is that today's manufacturing research is rendering ways to produce titanium wire more cost-effectively. New Ti alloys, specific manufacturing techniques, and increases in the overall production rate of titanium are steadily driving its cost down.
The other consideration in the big picture view of titanium is the cost of return in real-world applications. For example, if a lightweighting program for a freight hauling truck employs titanium springs, and those springs contribute to weight savings and subsequent energy savings in operating the vehicle, then the cost of premium alloys like titanium may be offset or negated (over time) by their performance in a particular application.
Spring Expertise
Titanium is a premium alloy worthy of consideration in a wide range of applications where size, weight, and performance are critical. Leading spring manufacturers, such as Newcomb Spring Corp, can manufacture custom springs from a variety of lightweight premium alloys, as well as offer expertise and assistance in specifying high-performance metals for specific spring designs and applications.
Need a quick way to evaluate spring design and performance? Check out Newcomb Spring’s free Springulator tool for smartphones and tablets, available at the App Store and Google Play.
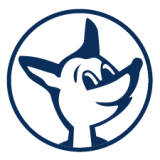