Custom Battery Springs & Contacts
Newcomb Spring specializes in delivering high-quality, precision engineered battery components tailored to your strict design requirements. We can produce a wide variety of shapes, configurations, and designs with an array of materials to choose from.
With more than a century of experience in spring design and manufacturing, our team is ready to assist with your order. We collaborate closely with you to enhance your custom battery spring and/or battery contact design, helping to reduce production costs and ensure optimal fit and functionality for your parts. Our custom battery spring and battery contact manufacturing team will deliver top-of-the-line products for your end application.
Get a Battery Spring QuoteBattery Spring & Contact Capabilities
Material Shapes & Sizes
- .002 to .625 inches (.005 to 15.875mm) in wire diameter
- Up to 0.063 inches (1.6mm) in flattened wire
- Round wire
- Square wire
- Flattened Wire
- Rectangular wire
- Special section wire
- and a large variety of materials available
Battery Spring & Contact Value Added Services
The following are only a portion of popular value added services we offer; this is not a comprehensive list. Please contact your local Newcomb Spring and discover what we can offer on your unique design.
Battery Spring and Contact Design Information
At Newcomb Spring, we provide design assistance to help bring your product to life—whether you need custom battery springs or precision aa battery connectors. Our experts don’t just review your design for cost reduction; we offer insights that enhance the functionality and fit of your part. From concept to prototype to full production, our team is here to support you every step of the way.
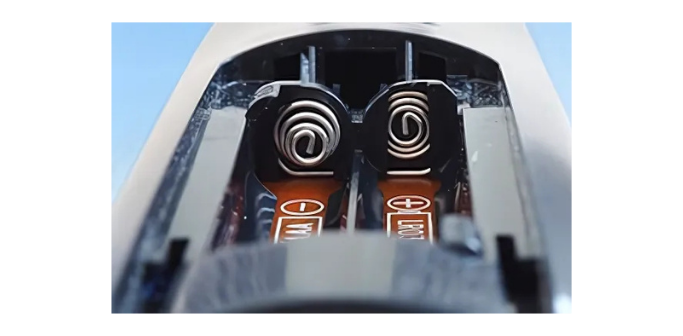
Battery Contact Design
A battery contact & spring typically performs two roles - to help provide pressure in order to hold batteries in place, as well as to conduct electrical current to the desired circuit. The force exerted by the spring on the battery often affects the electrical conductivity, especially where surface oxidation on the battery contacts may be present. Corrosion and oxidation, as well as the battery spring’s suitability for specific soldering processes, should be considered during design.
Newcomb Spring can assist in optimizing your battery component design’s:
- Conductivity
- Durability and Life Span
- Corrosion Resistance
- and Performance
Battery Spring & Contact Materials
Material Conductivity
Conductivity is a critical factor in the performance of battery springs and contacts, directly affecting the efficiency, power output, and life span of the battery. Selecting the right material for your design is essential, as different metals and finishes offer varying levels of conductivity, durability, and corrosion resistance.
Why Material Conductivity Matters
The choice of material directly influences the efficiency of power transfer and the stability of the battery connection. By carefully selecting the material, you can achieve an optimal balance between conductivity, durability, and cost, ensuring that your battery springs and contacts meet the specific demands of your application. Here’s a quick breakdown of a few common materials we offer, but make sure to contact us for a more in depth conversation of optimal materials for your design.
Commonly Requested Materials
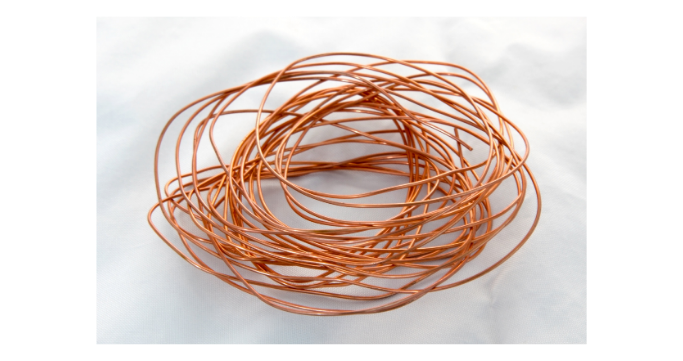
Beryllium Copper
High Conductivity: Copper is one of the most conductive materials available, making it ideal for applications requiring efficient power transfer
Get a quote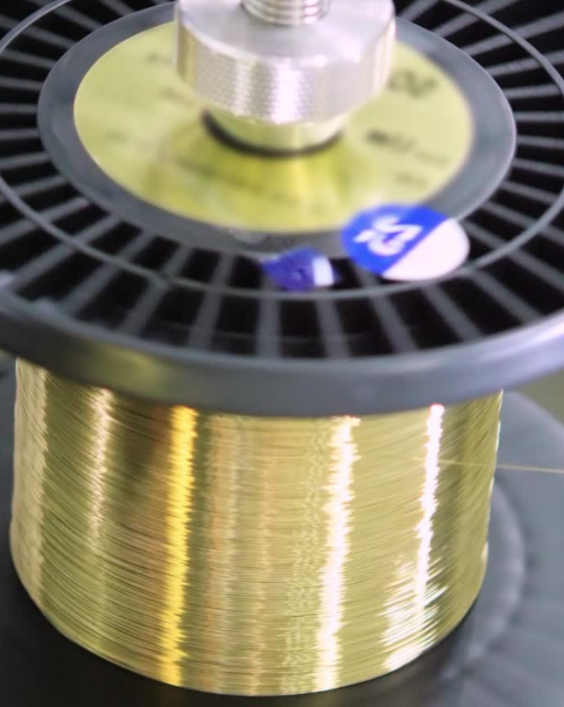
Spring Brass
High Corrosion Resistance: Spring brass has good conductivity, high corrosion resistance, and is easily formed, making this a great option for electrical applications that may encounter moisture
Get a quote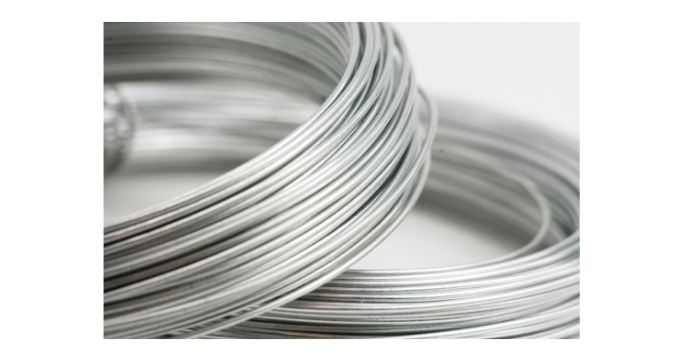
Nickel-Plated Carbon Steel
High Corrosion Resistance and Added Durability: Nickel-plated steel offers good conductivity while enhancing the durability and corrosion resistance of the component
Get a quote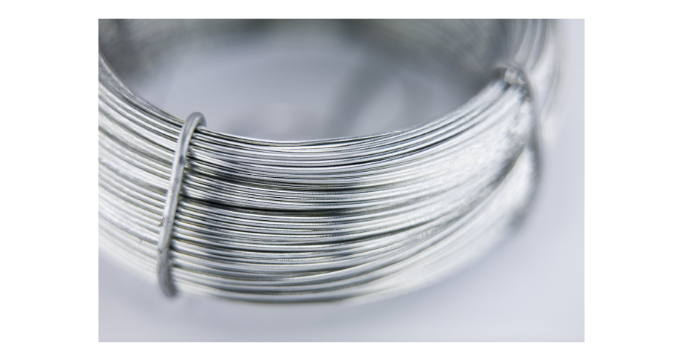
Stainless Steel
High Strength but Lower Conductivity: While not as conductive as copper, stainless steel is highly durable and corrosion-resistant, making it suitable for applications where durability is more critical than conductivity
Get a quote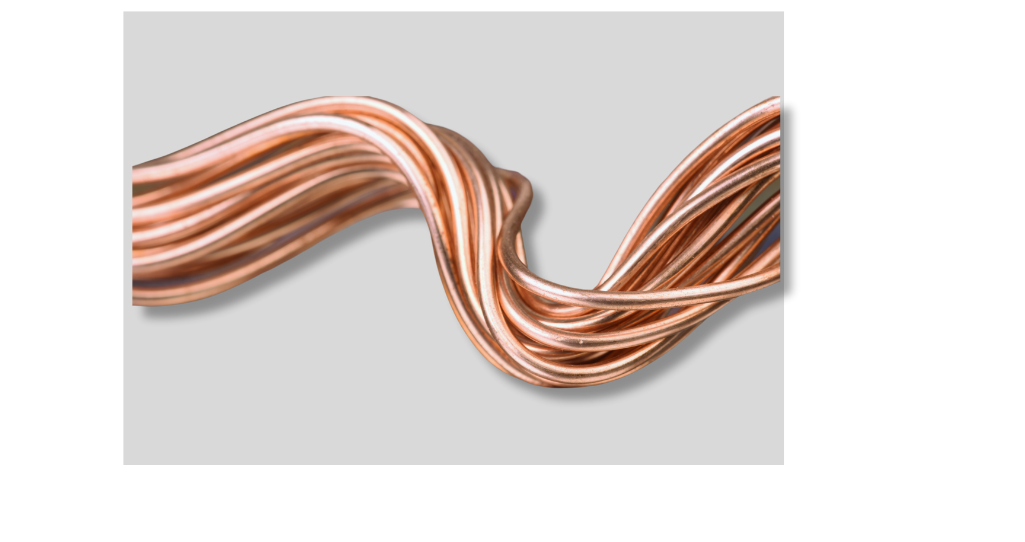
Phosphor Bronze
High Fatigue Resistance and Conductivity: An overall balanced material, praised for it’s well-rounded strength, corrosion resistance, conductivity, formability, and cost.
Get a quoteProduct Gallery
Below are just a small selection of the battery springs and contacts we have produced, including:
- AA Battery Contacts &Springs
- AAA Battery Contacts & Springs
- Battery Terminal Connectors
- Battery Spring Contacts
- Coil Springs
- Cylindrical Battery Contacts & Springs
- Wave Springs
- Constant Force Springs
- Contact Plates
- Contact Tabs
- Flat Springs
- Metal Strips
- Spring Loaded Electrical Contacts
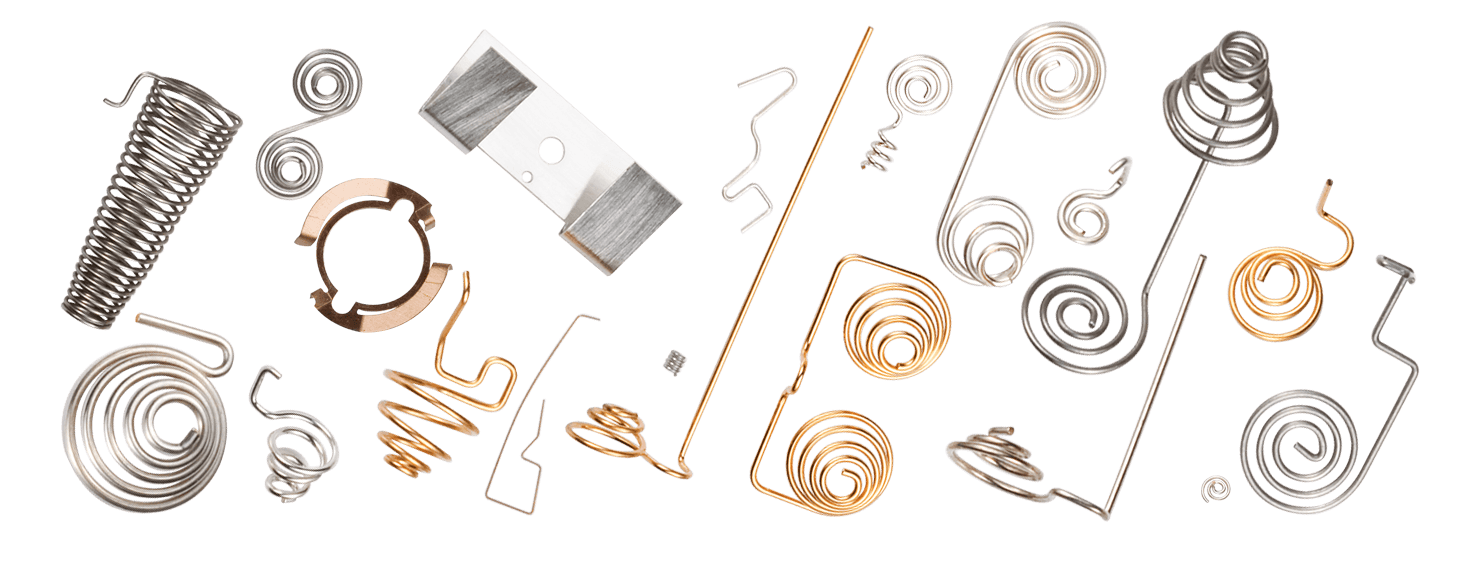