Constant Force Springs
- Originally Published by Newcomb Spring
Understanding the physics behind constant force springs and how “constant” force is derived.
As you walk into your office building on the way to work each day, or into your local bank, or any commercial facility, you probably pull open a heavy glass door. As you pass across the threshold, the door closes behind you. You don't give it a second thought. However, that heavy glass door was probably closed by a constant force spring. Constant force springs are used in a wide range of everyday applications. From door closers to cord and hose retractors, to exercise equipment, toys, electric motors, and more, constant force springs are at work applying force with amazingly high frequency and consistency. Let's take a closer look at the basic physics behind constant force springs.
In the 17th century, British physicist Robert Hooke outlined a formula for force and elasticity that is now known as Hooke's Law. Hooke's Law states that the force (F) needed to extend or compress a spring by some distance (X) changes in a scaled linear relationship to that distance. The formula is F=kX, where k is a constant that represents the stiffness of the spring.
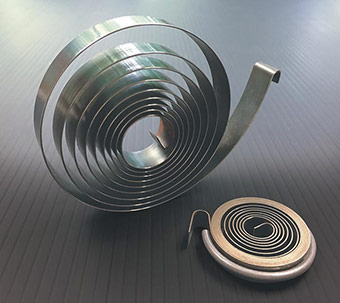
Hooke's law is nominal in terms of real spring performance. In the equation, X, the distance the spring moves, is meant to be a relatively small number. Ultimately, any elastic body that is stretched or compressed beyond the stress limits of its material composition shows signs of deformity. Force properties that rely on a state of consistent shape and tension will, therefore, change in a deformed state.
Ideally, constant force springs would apply consistent force over a given range of motion, repeatedly without change. In reality, constant force springs, like all elastic bodies, are limited by the stress limits of their materials. They deform if pushed beyond the limits of material stress or begin to weaken as their material fatigues over time. So, Hooke’s Law does apply to constant force springs. However, it is the way constant force springs are made, and their particular physical properties, that lead to the terminology "constant force." By taking a closer look at the physical properties of constant force springs, we can better understand how the name constant force is derived.
Commonly made of steel, constant force springs are manufactured by wrapping a flat piece of steel around a drum, or by coiling a steel ribbon around itself (with a virtually constant radius). The spring is mounted in its application, and one end of the spring is attached to a load. The spring exhibits torque forces when movement of the load causes the spring to wind against its resting state. The spring wants to return to its resting state, so it exerts force against the load.
In application, constant force springs rest in a pre-tensioned state. The act of coiling a ribbon of steel around itself, or wrapping it around a drum, puts the structure in a state of tension. If one were to measure the force of the spring in this state of tension, it would not be zero. In other words, constant force springs have a measurable force in the resting position. When the load moves against the spring, the spring moves a relatively short distance in a circular direction (most commonly in the direction of the initial wind, resulting in a small decrease in diameter). If we compare the springs force value in the loaded state versus its force value in the resting state, we find the difference in force to be relatively small. In more general terms, outside of the realm of physics, the small difference in force between the spring’s resting state and loaded state is considered insignificant. The spring’s force is, therefore, termed to be “constant.” In reality, constant force springs apply near constant force.
Constant force springs reach maximum rated load when the deflection distance reaches 11/4 times the spring's diameter. The width and thickness of the spring material and the diameter of the spring's outer coil generally determine load rating. In most cases, constant force springs are designed to provide force by turning in the same direction as their initial wind. Unless specifically designed to do so, reverse winding a constant force spring usually causes deformation.
Constant force springs can operate effectively for long periods of time. Most can function from thousands to millions of cycles before material fatigue reduces their effectiveness. Constant force springs are ideal for applications such as commercial door closers where tens of thousands of people may pass through a building's doorway each year.
There are numerous, essential engineering parameters to consider when designing or specifying a constant force spring. Materials, fatigue life, tensile load, torque and friction, speed and acceleration, mounting, safety considerations, and application environment are all critical factors.
The knowledgeable spring engineering staff at Newcomb Spring can help refine constant force and other spring designs to deliver optimum performance in any application. Learn more about our spring manufacturing capabilities, or contact the plant closest to you today.
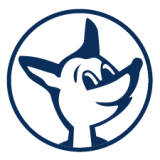