Unlocking Precision: Autoinjector Springs
- Originally published by Abbi Gillette
What are autoinjectors?
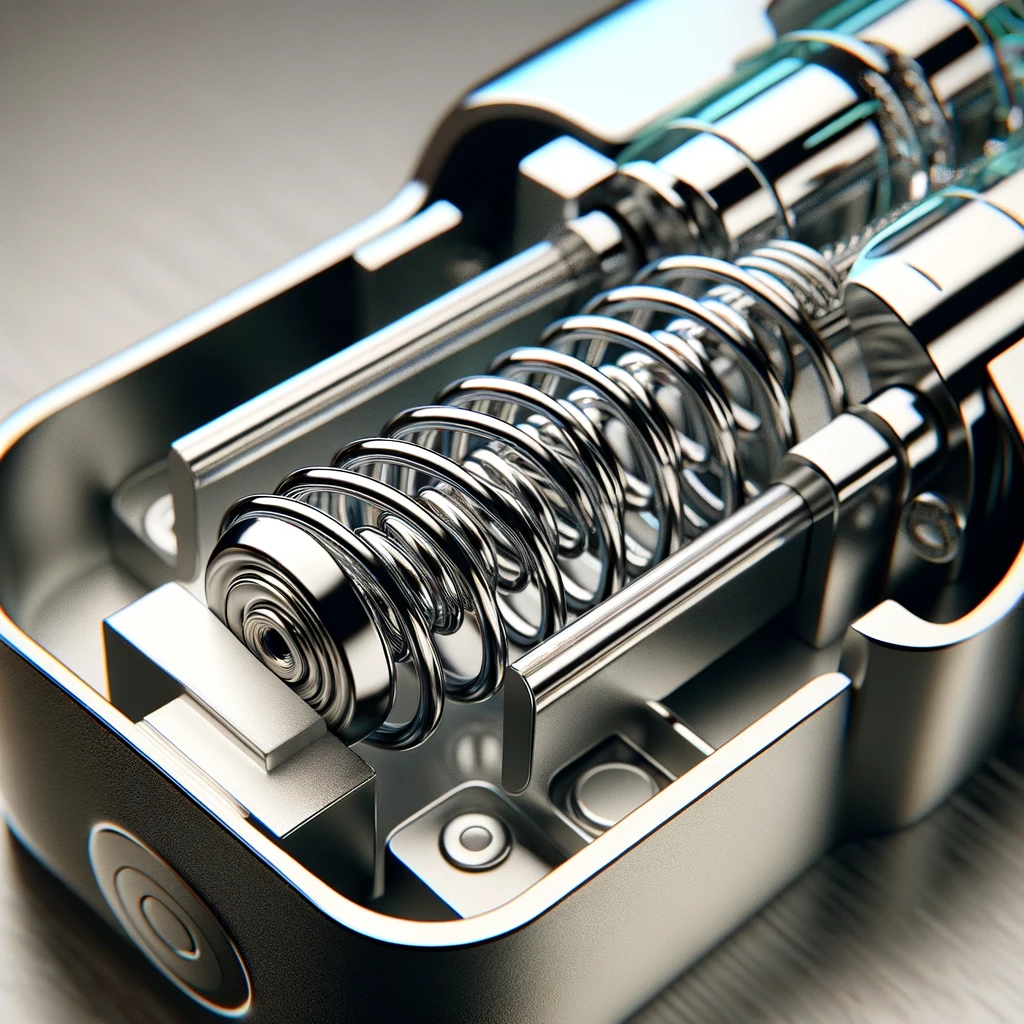
An autoinjector is a self-injectable device used to deliver a dose of medication. The ease of use and reliability of the product have assisted in lifting the intimidation that comes with self-administering an injection at home or in an emergency setting, making this an increasingly popular tool in the medical field.
Today, autoinjectors have become indispensable across a wide range of applications. They are not only used in treating acute conditions like anaphylaxis, migraines, and rheumatoid arthritis, but in an array of many other medical needs such as for weight loss drugs. As the diversity among the types of prescriptions being used inside the injectors continue to increase, so do the number of distinctive components needed for them. It becomes even more important to manufacture precision components that strictly conform to required specifications needed for each unique device.
What is Newcomb Spring's role in autoinjector manufacturing?

Most autoinjectors are spring-loaded devices, which means that the compression spring is pre-loaded, i.e. already compressed, before use. When the device is activated, the spring decompresses to its natural state and applies force to the plunger, which then pushes the needle and solution through the skin to the correct depth the drug needs to be released into.
The compression spring used within the injector plays a vital role in its success. As various drugs are used with the device, the spring specs must be redesigned to best fit the viscosity of the substance. If it is not produced within spec, this can cause an array of serious issues. For example, the needle might not be injected at the correct depth, or the substance might not administer at the correct speed or dosage. It must be meticulously designed and manufactured for precise and consistent results. With Newcomb’s extensive expertise and available design assistance, we can manufacture precision autoinjector springs to achieve the high-quality standards required for safe medical use.
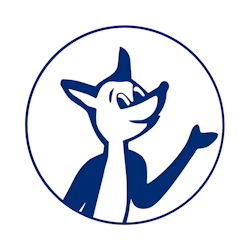
Newcomb Spring played a crucial role in designing and manufacturing the spring component for the world’s first self-retracting syringe.
Inventor, Dr. Sakharam Mahurkar, collaborated directly with Jason Bingham, the current General Manager of Newcomb Spring of Tennessee, for design assistance and to bring this idea to life. Jason recounts how passionate the late Dr. Sakharam was about making a product that would grant safety for him and other providers while handling needles. The design was granted a patent on May 5, 2009 under the title of Universal Safety Syringe. This invention has helped to prevent accidental exposure to biohazardous substances in the medical field, and Newcomb is proud of its contributions to the project!
Why our expertise sets us apart
Autoinjector springs require precision engineering and manufacturing to produce the highest quality, medical-grade product. Newcomb Spring has more than a century of manufacturing experience and teams of dedicated experts in the spring design field, and has a history of autoinjector spring manufacturing that is still going strong today. With our strict quality control measures, we can ensure each spring meets the required specifications and strict tolerances of your design.
As advancements in this technology continue to develop, we want to be at the forefront of innovation. Our Kando Tech Centers are dedicated to engineering a perfect spring design for your custom needs. Whatever the challenge, Newcomb wants to be your go to! Request a quote today or contact sales@newcombspring.com for more information.
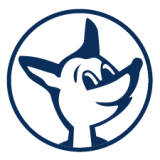