Compression Spring Operating Stress: Static Conditions
Compression Spring Design Resources – Spring Performance
For static applications, the yield strength or stress relaxation resistance of the material limits the load-carrying ability of a spring. The spring is required to operate for a limited number of cycles, and the velocity of the end coils is low to preclude high stresses due to surging or impact conditions. Maximum allowable torsional stress for compression springs used in static applications is presented in Table 21 as a percentage of the tensile strength for common spring materials. For springs that do not contain beneficial residual stresses induced by set removal, maximum allowable torsional stress values are from 35 to 50% of the tensile strength. To calculate the stress before set removal, it is necessary to use the maximum percentage of tensile strength before set removal correction factor. If the calculated stress at solid is greater than the indicated percentage of tensile strength, the spring will take a permanent set when deflected to solid. Amount of set is a function of the amount that calculated stress at solid exceeds the indicated percent of tensile strength.
To increase the load-carrying ability of springs in static applications, it is common practice to make the spring longer than its required free length and to compress the spring to solid. This causes the spring to set to the desired final length and induces favorable residual stresses. This process is called "removing set" or "presetting" and can be conducted at either room or elevated temperatures. The loss of deflection from the free position to solid by cost set removal should be at least 10%. If the set is less, it is difficult to control the spring’s free length. Ratios of stress greater than 1.3 lead to distortion and do not appreciably increase the load-carrying ability.
Allowable torsion stresses in springs with set removed are significantly higher than springs that have not had set removed. It is important to note that, because yielding has occurred during presetting, the stress is relatively uniform around the cross section and it is calculated using the "maximum percentage of tensile strength after set removed" stress correction factor. Set removal is an added spring making operation that increases the manufacturing cost but greatly increases the premium materials. In some instances, springs have the set removed during an assembly operation.
If the calculated stress using the "maximum percentage of tensile strength after set removed" stress correction factor exceeds the percentage of tensile strength allowed, the spring cannot be made. In this case, it is necessary to either lower the stress by altering spring design or selecting a higher strength material.
In some applications, maximum operating stress is limited by material stress relaxation resistance and amount of load loss that the design can tolerate. When load is constant, these designs are limited by material creep resistance. When the spring is compressed at a fixed test height, stress relaxation resistance of the material is limiting. Designs limited by stress relaxation resistance are more common than designs limited by creep resistance. It is suggested that creep-limited designs be reviewed by a qualified engineer with spring making experience.
Stress relaxation is defined as percent load loss according to the following relationship:
% Relaxation = (PO – PF / PO) X 100
Typical stress relaxation data indicates that at high stresses, some spring materials, such as music wire, exhibit appreciable stress relaxation after only 100 hours at temperatures as low as 212° F (100° C). Stress relaxation is affected by material, spring processing variables, time, temperature and stress.
When set is removed at an elevated temperature, the process is called "heat setting". It significantly improves the stress relaxation resistance of springs at moderate temperatures and is frequently a more cost-effective method for achieving low levels of stress relaxation than specifying a costlier spring material.
Content Copyright Spring Manufacturers Institute, Inc.
This information is attributed to, and provided courtesy of, the Spring Manufacturers Institute, Inc. (SMI). Newcomb Spring and SMI provide this as advisory information only, and disclaim any and all liability of any kind for the use, application or adaption of material published on this web site.
Resource Illustration
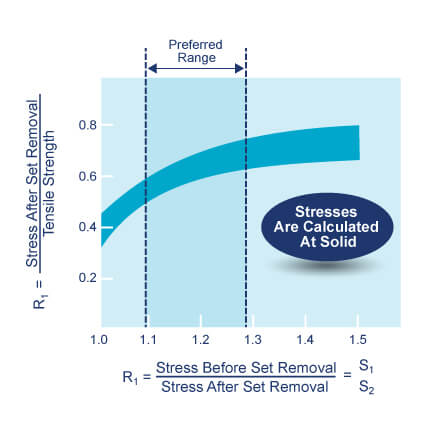
The loss of deflection from the free position to solid by cost set removal should be at least 10%. If the set is less, it is difficult to control the spring’s free length. Ratios of stress greater than 1.3 lead to distortion and do not appreciably increase the load-carrying ability.